Dossier IoT et automobile : les constructeurs pied au plancher
Publié par Jacques Cheminat le | Mis à jour le
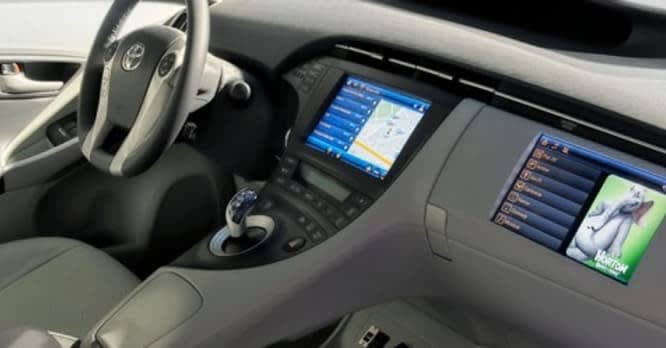
Le monde de l’automobile est bousculé par l’Internet des objets. La rédaction de Silicon.fr s’est penchée sur les deux aspects de cette révolution au sein du secteur automobile : l’impact sur les voitures et celui sur les industriels.
I-L’automobile à l’heure de l’autonomie
Il y a deux ans, le Mondial de l’Auto 2014 consacrait l’essor de la voiture connectée. Les solutions de couplage entre le système d’infotainment de la voiture et les smartphones d’Apple, Google et MirrorLink faisaient alors l’événement. Depuis, cette fonctionnalité s’est banalisée et l’arrivée de Google ou Apple dans la voiture ne s’est pas encore réalisée. « Il est difficile de savoir comment les choses vont évoluer », explique Thierry Viadieu, directeur de programme Véhicule Connecté et Autonome Renault. « Même si Google travaille dessus, Android est encore loin d’être un OS possible pour une voiture. Ils le reconnaissent eux-mêmes, c’est un challenge très compliqué que de gérer une voiture qui soit connectée, autonome en temps réel. Les prochaines générations de véhicules attendues dans les années qui viennent ne seront pas sous Android. »
Depuis 2014, la voiture connectée s’est taillée une place significative sur le marché français. « Nous avons déjà vendu des centaines de milliers de véhicules disposant de cette connectivité », confie le responsable chez Renault. « R-Link est monté en strandard sur un certain nombre de modèles Renault. Sur Captur, le taux de montage de cette option est de l’ordre de 30%. » Son rival Yves Bonnefont, Directeur Général de la marque DS chez PSA surenchérit : « Historiquement le groupe PSA a fait le choix de connecter beaucoup de ses voitures dans une logique d’appel d’urgence. Nous avons aujourd’hui sur la route plus d’un million de voitures ainsi connectées. En cas de crash, l’airbag se déclenche et la voiture transmet automatiquement les coordonnées GPS du véhicule à un centre de secours qui va appeler le conducteur et, en cas de besoin, envoyer les secours. C’est une utilisation assez basique de la voiture connectée, mais bien d’autres services vont suivre. »
Pas de voiture 100% autonome avant 2025
Google, Apple ou Microsoft ne sont pas encore parvenus à imposer leur présence dans l’industrie automobile et, cette année encore, Google n’était pas sur le salon de Paris. C’est un autre californien qui occupe pourtant les esprits de tous les constructeurs. Ce californien, c’est Tesla Motors. Avec 24 500 véhicules vendus au troisième trimestre 2016, les volumes de Model S et de Model X produites à Fremont restent encore anecdotiques comparés aux millions de véhicules qui sortent des chaines d’assemblage des grands constructeurs mondiaux. Néanmoins Tesla monopolise l’attention des médias. Les débuts du mode « Autopilot » ont fait couler beaucoup d’encre et actuellement tous les constructeurs traditionnels et leurs équipementiers testent leurs propres systèmes de conduite semi-autonome. Illustration de cette course technologique, Valeo qui, quelques jours avant le Mondial, a fait tourner une voiture équipée de sa technologie de conduite Cruise4U pendant 24 heures d’affilée sur une route particulièrement hostile : le périphérique parisien. Le véhicule est ressorti entier de ce test particulièrement difficile.
Plutôt que proposer une voiture autonome le plus rapidement possible, les constructeurs préfèrent offrir des fonctions d’aide à la conduite de plus en plus sophistiquées sur leurs véhicules actuels. « Nous auront l’autonomie totale vers 2025 », estime Pierre Jalady, directeur marketing de BMW France. « Avant cette date, je ne vous conseillerais pas de lâcher le volant ! Cela étant nous faisons évoluer la technologie des assistants de conduite si bien que dès aujourd’hui on peut conduire avec le régulateur de vitesse actif et le système de suivi et changement de ligne automatique, ce qui permet de se déplacer sur 80% du trajet en mode autonome. Atteindre le 100% va demander encore un peu de temps. » Pour l’heure, les constructeurs automobiles traditionnels ont été pris de vitesse par Tesla dans cette course à la voiture autonome. Mais ceux-ci espèrent à mots plus ou moins couverts un retour de bâton pour le californien. Chaque accident de Tesla est désormais très largement médiatisé et une enquête est ouverte en Allemagne sur la dangerosité de l’Autopilot Tesla.
Tous les grands constructeurs mondiaux testent leurs véhicules autonomes en secret ou sur route ouverte et un consensus se fait sur l’échéance de 2025. Présenté à Paris, le concept car ID de Volkswagen est une voiture électrique qui devrait concurrencer les Nissan Leaf et Renault Zoé vers 2020. Néanmoins, l’allemand envisage déjà une version autonome dont le volant viendra se rétracter dans le tableau de bord. Le constructeur allemand espère commercialiser cette version autonome à partir de 2025.
Les mises à jour logicielles « Over the Air » vont s’imposer
Si la conduite autonome de Tesla fait beaucoup parler d’elle, ce qui impressionne le plus ses concurrents, c’est une capacité qui pourrait sembler secondaire, ses mises à jour logicielles par réseau. « La connectivité est maintenant une nécessité sur les mises à jour de logiciels pour le conducteur comme pour le constructeur », explique Dominique Doucet, product marketing director de Valeo, en charge chez l’équipementier de la feuille de route relative au véhicule connecté, au véhicule autonome et aux interfaces homme-machine.
« Aujourd’hui quand on regarde les coûts de rappel des véhicules, la part du logiciel justifie complètement le déploiement massif des mises à jour over the air. Le business model est là. Avec une voiture telle que la Tesla, la connectivité fait totalement partie de la voiture. Le constructeur imagine une nouvelle économie autour de la data, de son exploitation CRM, et la machine est maintenant en marche. »
Une connectivité généralisée entre les véhicules et les routes
Mercedes a aussi profité du Mondial de Paris pour présenter sa Generation EQ, concept car qui préfigure la gamme de véhicules électrique que prépare l’allemand pour les années 2020. Une dizaine de véhicules devraient étoffer cette nouvelle gamme entre 2020 et 2025. Si l’allemand, pourtant très en pointe dans la voiture autonome, n’a pas formellement annoncé de version autonome de son EQ, celle-ci se distinguera par sa capacité de communication de type V2V et V2I très avancées. Ce sera l’une des grandes tendances des prochains salons automobiles. Les voitures vont échanger des données, non plus seulement avec le constructeur, mais entre-elles et avec le réseau. C’est ce que l’on nomme le V2V (Vehicule to Vehicule) et le V2I (Vehicule to Infrastructure).
Déjà Audi commercialise certains modèles haut de gamme, Q7, A4 et A4 Allroad 2017, dotés de tels boitiers de communication. Ces transmissions de données entre la route et la voiture permettent à celle-ci d’afficher la durée d’attente à un feu rouge ou mieux encore réguler sa vitesse pour ne plus devoir s’arrêter aux feux rouges. Un réseau WiFi spécifique a été standardisé à cet effet et aujourd’hui les constructeurs, équipementiers et autorités travaillent à la standardisation des messages. Les voitures pourront se prévenir les unes les autres en cas de route glissante détectée grâce à l’ESB du véhicule et une alerte peut être transmise aux véhicules en cas d’accident. De tels systèmes permettront un jour d’éviter les carambolages dès lors que tous les véhicules disposeront de telles capacités de transmission.
La virtualisation des calculateurs, une idée qui tient la route
Si les ingénieurs s’en donnent à cœur joie pour rendre leurs véhicules de plus en plus évolués, cela à un impact très direct sur la complexité du véhicule qui se voit bardé de capteurs, de calculateurs. Le nombre de lignes de code a explosé ces dernières années avec des logiciels pour l’infotainement, mais aussi pour faire tourner le moteur, pour gérer les freins, les systèmes optiques, etc. Une voiture de luxe compterai ainsi 100 millions de lignes de code. A comparer aux 25 millions de lignes de code de l’avion de combat F-35 ou aux 12 millions d’Android.
Devant une telle masse de code, les mises à jour OTA deviennent indispensables pour maintenir les logiciels à jour et corriger les bugs sans devoir obliger l’automobiliste à passer en concession. Outre le prix de la maintenance, cette multiplication du nombre de calculateurs embarqués a un effet très direct sur le coût de la voiture. La multiplication des aides à la conduite et autres fonctions communicantes ne vont qu’accroitre ce besoin en puissance de calcul embarquée. L’idée de virtualiser puis réunir tous ces calculateurs dans un seul boitier commence à faire son chemin dans le secteur automobile comme cela commence à être le cas dans le secteur aéronautique.
Altran et Jaguar Land Rover se sont associés pour créer CoherenSE. Il s’agit d’un middleware permettant d’exécuter plusieurs environnements d’exécutions et systèmes d’exploitation temps réels et hyperviseurs. Si l’approche semble séduire les constructeurs, ceux-ci estiment que pour des raisons de sécurité, la distinction entre systèmes d’infotainement et systèmes embarqués liés au fonctionnement même de la voiture restera bien séparée.
La voiture devient un composant du smart grid global
Parmi les concepts car les plus étranges de ce salon figure en bonne place le Toyota FCV Plus. Le petit véhicule électrique fonctionne à l’hydrogène, une technologie chère à Toyota mais qui semble désormais en perte de vitesse sous la pression des voiture électriques à batterie Lithium-Ion. Le gros intérêt du concept nippon, c’est que la pile à combustible qui l’alimente peut fort bien être utilisée comme un générateur électrique afin d’alimenter une maison ou plus généralement devenir un composant d’un smart grid global.
Le groupe Renault/Nissan va dans le même sens avec le programme Leaf for home. La batterie de la voiture est utilisée par le réseau électrique pour stocker de l’énergie aux moments de forte production, lorsque l’ensoleillement ou le vent est le plus fort. Puis il va alimenter le circuit électrique de la ville lorsque la consommation électrique est plus élevée. Le concept n’est pas totalement nouveau, le programme « Leaf for Home » a été dévoilé pour la première fois en 2014. Maintenant que le parc de véhicules électriques, et donc la capacité de batteries installée totale s’accroit, la solution commence à avoir du sens à l’échelle d’une ville.
II-Les ateliers prennent le virage du numérique
Les français l’appellent l’industrie du futur, « Industry 4.0 » outre Rhin. Avec la voiture connectée l’industrie automobile connait une évolution majeure de ses produits mais aussi du côté de la production.
Yann Vincent, directeur industriel de PSA Peugeot Citroën résume le défi qui se pose aujourd’hui à toute l’industrie automobile : « La question de l’efficacité de notre système de production est une question permanente pour nous. Nous sommes dans une industrie qui est extrêmement compétitive et dans laquelle on ne peut à aucun moment s’endormir sur ses lauriers et nous sommes à l’affut de toute initiative, toute solution qui puisse modifier la manière dont nous fabriquons nos voitures. Nous avons fait le constat qu’après des dizaines d’année où finalement les progrès réalisés dans les process automobiles ont été amenés par ce que l’on appelle le Kaizen, avec le concept d’amélioration continue avec des robots sans cesse plus performants, mais aujourd’hui nos assistons à des ruptures technologiques qui peuvent changer considérablement la manière dont nous fabriquons nos voitures et nous opérons nos usines. »
Fabrication additive, réalité virtuelle, réalité augmentée, robotique collaborative et objets connectés, les industriels suivent de nombreuses pistes pour améliorer à la fois la productivité de leur outil industriel mais aussi sa flexibilité afin de réduire le « Time to market » de leurs nouveaux véhicules. Pierre Jalady, directeur marketing de BMW France, commente l’approche du constructeur allemand : « Nous voulons couvrir l’ensemble de la chaine de valeur, de la production jusqu’aux clients, la voiture connectée, les concessionnaires, avec cette connectivité. Notre usine de Leipzig où nous avons déployé des systèmes autonomes connectés, des systèmes de productions entièrement automatisés et connectés comme pour la BMW i3, nous permet un assemblage de la voiture par collage. La CAO nous permet aujourd’hui d’avoir des inserts dans nos voitures qui sont conçus sur mesure et produits par impression 3D directement dans nos usines de montage. Certaines pièces mais aussi des outils sont ainsi réalisés à la demande en impression 3D, au moment où on en a besoin. Cela évite d’avoir à les stocker. C’est aussi le cas pour des pièces qui sont épuisées en stocks et que nous sommes capable de produire à nouveau en très faibles quantités pour nos anciens modèles. »
Les robots gagnent en intelligence et en autonomie
Si les constructeur automobiles ont lourdement investi dans la robotique dès la fin des années 70, la mise en place d’un atelier de ferrage où sont soudées les « caisses en blanc », c’est-à-dire la structure des véhicules, les chaines de montage ou encore les ateliers peinture, implique une programmation très précise de centaines de robots. L’investissement initial est très important et toute modification est coûteuse. Une nouvelle génération de robots est en train de se frayer une place dans les ateliers. Ce sont les robots collaboratifs. Moins puissants, moins rapide que bien des robots industriels classiques, ces robots présentent deux atouts. D’une part, ceux-ci ne nécessitent pas la mise en place d’une cellule de protection pour sécuriser de leurs mouvements, en outre, il n’est plus nécessaire de les programmer. Il suffit à l’ouvrier de lui montrer le mouvement à accomplir pour que celui-ci se reprogramme. Ce type de robot peut être mis en service afin de travailler sur les mêmes postes de travail que les ouvriers et changer un tel robot de poste ne nécessite que quelques minutes. Volkswagen a déployé de tels robots dans son usine de moteurs de Salzgitter dès 2013.
Depuis, les autres constructeurs allemands ont suivi et ont déployé à leur tour ces robots mais déjà une autre catégorie de robots arrive, les robots d’infragistics. A la manière des robots qu’Amazon a déployés dans ses entrepôts pour aller chercher les marchandises, les constructeurs automobiles mettent en place des robots autonomes qui amènent les pièces comme les moteurs, les équipements en bordure des lignes d’assemblage. Le français Balyo propose déjà depuis quelques années des chariots de manutention robotisés tandis que Segula Technologies a dévoilé sur le Mondial de l’Auto un tel robot. Là encore, les constructeurs allemands ont pris de l’avance, à l’image d’Audi qui s’est tourné vers Serva Transport Systems pour utiliser les robots RAY dans son usine d’Ingolstadt.
Ces robots prennent en charge les véhicules assemblés à la sortie de la chaine de montage et vont les stocker dans les parkings de l’usine en attendant leur livraison. Pierre Jalady, directeur marketing de BMW France ajoute : « Nous avons aussi dans nos ateliers des modules autonomes capables de se déplacer de façon autopilotée pour fluidifier la production. Pour nous, le Manufacturing 4.0 est une réalité dès aujourd’hui. C’est une opportunité pour améliorer encore l’efficacité de notre production, mais c’est aussi la capacité de personnaliser nos produits. »
La réalité augmentée trait d’union entre l’homme et la production numérique
Les opérateurs humains sont eux aussi de plus en plus intégrés à cette continuité numérique recherchée par les constructeurs à l’aide de nouveaux outils connectés. Les constructeurs misent beaucoup sur la réalité virtuelle et la réalité augmentée pour accélérer les phases de conceptions de leurs véhicules mais aussi simplifier le travail de montage et contrôle qualité. Yann Vincent détaille la problématique pour le groupe PSA Peugeot Citroën : « Comment apporter une assistance à nos opérateurs au travers de la réalité virtuelle, comment lui apporter une assistance sur des travaux qui sont pénibles, comment faire travailler les opérateurs aux côtés des robots et augmenter considérablement la flexibilité de notre appareil de production, ce sont des choses qui nous intéressent, de même qu’avoir une continuité numérique depuis la phase de conception du produit jusqu’à sa fabrication, puis sa maintenance. »
La réalité virtuelle s’est rapidement fait une place dans les bureaux d’études des constructeurs automobiles. A partir des modèles 3D issue de la CAO, le modèle 3D peut être testé en simulation numérique mais aussi en réalité virtuelle dans des caves de réalité virtuelle. Designer mais aussi ingénieurs de conception et spécialistes de l’industrialisation et de la maintenance peuvent travailler sur un véhicule avant même que le premier prototype de la voiture ne soit construit. Cette approche 100% numérique à trouvé avec l’impression 3D un moyen de créer les premières maquettes et les pièces prototypes. Un outil qui permet, là encore, de réduire les temps de conception de manière spectaculaire. Gordon Murray Design annonce ainsi une réduction de 68% de son temps de prototypage pour sa voiture T.25 depuis la mise en production d’une imprimante 3D.
Après la réalité virtuelle, les industriels s’intéressent désormais à la réalité augmentée non plus pour les bureaux d’études mais pour les ateliers. Le français Diota, spinoff du CEA spécialisée dans la réalité augmentée, a mis au point un système de projection qui affiche sur la pièce les tâches à accomplir comme les perçages ou l’ajout d’éléments. La solution a été déployée chez Dassault Aviation avant de séduire les constructeurs automobiles à leur tour. Diota compte Faurecia, Renault, PSA, Daimler, Volkswagen et Porsche parmi ses clients. Lionnel Joussemet, PDG de Diota explique cet intérêt porté à la réalité augmentée par les industriels : « On parle d’industrie du futur, mais les opérateurs qui sont sur le terrain disposent de peu de données issues du système d’information. Nous développons des systèmes basés sur différents dispositifs comme les systèmes projectifs, les tablettes numériques et prochainement les lunettes de réalité augmentée qui vont permettre de restituer des informations de manière intelligible et ergonomiques toutes les informations qui aujourd’hui sont délivrées via des fiches d’instruction papier. Le système projectif affiche sur la pièce les opérations à réaliser. Quatre secteurs s’intéressent aujourd’hui à cette approche : l’industrie lourde comme l’aéronautique, la construction navale et le ferroviaire, l’automobile et enfin l’industrie chimique.»
Les réseaux IoT arrivent dans les ateliers
L’Internet des objets est aussi une piste d’amélioration des processus de production suivie par les constructeurs automobiles et leurs équipementiers, mais la sécurité reste un frein majeur dans l’industrie. Comme l’a montré l’attaque du ver Stuxnet sur les installations nucléaires iraniennes en 2010 ou encore la cyberattaque réussie contre les centrales de production énergétiques ukrainiennes en 2016. Les installations industrielles sont très vulnérables. Les industriels se refusent à interconnecter leur réseau internet industriel avec le réseau IT de l’entreprise. Certains se tournent même vers des systèmes de pont réseau industriel, comme le Datadiode de Foxit, pour assurer une étanchéité matériellement totale entre les deux mondes.
Beaucoup préfèrent déployer des réseaux de capteurs exploitant les réseaux sans fil, que ce soit des réseaux LPWAN comme Sigfox ou LoRa ou même des réseaux mesh 802.15.4. Nicolas Bonnin, directeur de Visian, start-up de Neurones IT positionnée sur les objets connectés souligne : « Deux problèmes se posent aux constructeurs automobile aujourd’hui. Avant de songer à l’IoT, il faut mettre en place des réseaux. Cela représente un coût très important et le niveau de sécurité des objets connectés actuel fait qu’ils veulent éviter d’utiliser leurs réseaux industriels. »
Pour Eric Poupry, directeur général en charge de l’IoT et de la cybersécurité de Factory Systèmes, le cas d’usage le plus fréquent de l’IoT dans l’industrie, porte sur les économies d’énergie. « Les constructeurs automobiles notamment ont déjà beaucoup automatisé leurs chaines de fabrication. L’IoT industriel ne vient donc pas pour remplacer les chaines d’acquisition de données déjà en place. L’IoT intéresse d’avantage les équipementiers, néanmoins ces industriels doivent mettre en place les normes ISO 50001 et 50002 et donc être capable de remonter leur consommation d’énergie. L’IoT permet de placer des compteurs d’énergie où l’on souhaite, sans devoir tirer de câbles dans l’atelier. Le coût moyen d’installation d’une prise réseau dans un atelier est de l’ordre 1500 euros par unité. Donc le coût d’un tel projet sur du sans fil est financé par les seules économies réalisées sur l’installation des câbles réseaux. »
Un autre projet mené par Factory Systèmes chez un constructeur automobile porte sur ce que l’on appelle l’appel à poste. Lorsqu’un opérateur va manquer de pièce il faut qu’il demande à être réapprovisionné sans devoir quitter son poste. « Dans une usine où il va y avoir entre 1 000 et 1 200 personnes qui ont besoin d’un bouton d’appel, tirer des câbles va coûter une fortune. La radio permet de mettre en place des milliers de boutons connectés avec une infrastructure très légère à des coûts très inférieurs à celui d’approches plus traditionnelles. »
Dès lors que le problème de la sécurité des réseaux de collecte de données sera résolu, les industriels vont pouvoir exploiter les données générées par leurs robots, automates et machines. Le Big Data va notamment leur permettre de passer à une maintenance préventive de leurs équipements mais aussi analyser ces données afin d’accroitre leurs processus de production. Bernard Lenssens, spécialiste BizTalk et IoT Azure chez Codit France souligne : « Installé sur un PC industriel, notre logiciel collecte les données issues des capteurs de température, humidité, pression, vibration, etc. Des données qui permettent de mettre en place de la maintenance préventive, prédire des pannes, etc. Nous avons mis en place du Machine Learning sur Microsoft Azure pour prédire quel moteur électrique doit être changé, que tel engrenage nécessite d’être lubrifié, etc. Nous cherchons à développer des solutions génériques. Nous regroupons les différents capteurs par étapes de production, par machine et cartographier la ligne de production. Bien souvent les industriels ont réalisé leurs premiers proof of concept mais nous pensons que les déploiements devraient être très rapides maintenant. »
Selon les analystes du cabinet spécialisé Roland Berger, la mise en œuvre de l’ensemble de ces moyens permettra aux constructeurs automobiles d’abaisser leurs coûts de production de 10 à 20%. Un gain énorme pour une industrie aussi concurrentielle que l’automobile et qui est l’une des plus en pointe dans la course à la productivité et la chasse aux coûts
Crédit Photo : Ngconnect via Visual Hunt